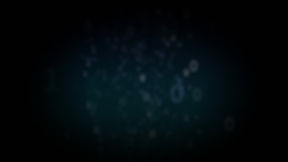
DIWALI ASSIGNMENT ON CALCULUS 2016
Assign By : Manish K Gupta Sir Course : SC 107
Caclulus :Where are you?
FALL 2016
DA-IICT,
GANDHINAGAR
​
​
​
​
Proporional-Integral-Derivative Controller
​
​
​
November 21, 2016
Abstract:
This project is from a topic Waves from Std. 12th of science. It is a device which controls the signal to a desired output...
1 INTRODUCTION:-
A PID controller also known as proportional, integral, derivative is a complicated and useful device.It has a loop control(uses it for repeatition) feedback mechanism which is used in all type of control systems. SO it’s main use is controlling, for example, output of wave. It continuously calculates as said now or makes a loop of an error value (depending on time) as the difference among a set-point, that is given, and a variable (That occurs during a process), which is measured and applies a correction based on proportional, integral, and derivativeness (normally said as P,I,D), which gives their name to some discrete controllers.
​
figure.1: Photo of an old PID from wikipedia
​
2 WORKING:-
A PID runs a loop to an error, as described in 1st para, e(t) as the difference between
set-point and a measured variable(U(t)) occuring in process and applies correction based on (P,I,D). The controller decreases the error over time by adjusting of a control variable U(t)(2nd variable), of a new value determined by the equation:
​
​
​
Are all positive and shows the coefficients of (P,I,D) terms.
In this model:
P=values of error at current time. Eg, if e(t) is big and non-negative, the output will be same. I=sets of the past error values. Eg, if present output is not strong, the error integral will be given a place over time, and it will respond by applying a stronger action.
D=possibility in future of error, based on its current rate.
As PID depends only on e(t), not on information of the lying process , it is mainly applicable, easy and useful. By tuning the three parameters of the model, it can work with the needed process requirements. The main principle of it can be showed in context of its answer to any given error, the number of times which the system repeats over a setpoint, and the number of times any system’s oscillations. The use of it’s algorithm does not give stability or optimal control of system.
Some people may require only one or two terms to provide the exact control system. This is done by taking all other parameters as zero. A PID device is called a PI, PD, P or I controller in the absence of one of the required actions. They all are usual, as derivative is sensitive for measuring voices, by the way the absence of integral can deviate the system from reaching its target to its destiny or value.
​
​
​
​
​
​
​
​
​
​
​
​
​
3 PID Theory
It describes the parallel (non-interacting) form of the PID.
Its three correcting terms name its control scheme, whose sum creates a new manipulated variable (mv). The P,I,D terms are added to calculate the output. By taking U(t) as output of it, the final part of it’s algorithm is
​
​
​
​
​
are proportional,integral and derivative gains, We were talking about error variable, it’s equation is: e(t) = SP − PV() is the error
SP is the setpoint, PV(t) is the process variable),
t is current time,
There is transfer function (w transfers values in the above both equations) in the Laplace domain (a typical domain of Process variable) of the PID controller is:
L(s) = Pk + Pi/s + Pds
where s is a complex frequency (not going in detail).
4 Proportional, Integral and Derivative Terms
The proportional (Pk) term produces an output (proportional to the current e(t)). The proportional response can be adjusted by multiplying the error the proportional gain Pk, called the proportional gain constant.
This proportional constant has a equation,
​
​
​
​
A high value of Pk results in a big change in output for a given change in e(t). If Pk is very big, the system can become unstable. In contrast, small value of Pk gives a small response in the output to a large input error, and a less responsive controller (Such a PID cannot be used). If Pk is too low, the controlling action can be very small while giving response to system disturbances.
The contribution from Pi is proportional to both value and duration of the error. The integral in a PID controller is the integration of instantaneous errors over time and gives the offset all together, that should have been corrected before. This error is then multiplied by Pi and added to the output.
The integration term is given by,
​
This term speeds up the movement of process towards the set-point and takes out the residual error at steady-state that occurs of a pure proportional controller. However, since Pi responds to calculated errors seen before, it can make the present value to change the
set-point value.
The value of contribution of the derivative term to overall process is named as Pd (derivative gain).
It’s equation is,
​
​
​
It predicts system’s behavior and improves stability of the system. Ideal derivative is not possible, so that implementation of PID includes a low-pass filtering for this term to limit the high-frequency gain and voice. This action is sometimes used in practise though by one estimate is only 25 percentage of deployed controllers because of its changing impact on stability in applications.
5 Stability of the controller(Important)
If the PID parameters are not taken correctly, the process input cannot be stable, with or without oscillation, and is stopped only by mechanical breakage. Unstability is caused by excess of gain, mainly in presence of lag.
Stabilization of response is required and process must not oscillate for any combination of process conditions and setpoints, though sometimes marginal stability (bounded oscillation) is acceptable.
Mathematically, the origins of unstability can be seen in the Laplace domain seen earlier.
The complete loop transfer function is:
​
​
P(s): PID transfer function
K(s): Plant transfer function
​
The system is called unstable where this diverges for some value of s. This happens for P(s)K(s)=-1. Basically, this happens when K(s)G(s)—=1 with a 180 degree phase shift. Stability occurs when K(s)G(s)¡1 for frequencies which suffers high phase shifts. A more general way of this effect is known as the Nyquist stability criteria.
6 Most Famous Applications
1: Automatic ship steering
2: Diaphragm operated valves(used in old days) 3: Discrete electronic circuits(various fields in it) 4: Disk drive(Head Positioning)
5: Power conditioning
6: Seismometer(motion detector)
7: Laser diode controllers(High bandwidth and low noise performance) 8: Distributed control systems(Modern industrial use)
9: Programmable logic controllers(Modern industrial use) 10: Panel Mounted digital controller(Modern industrial use) 11: Temperature controller
12: Plastic injection machinery
References
[1] M. Araki.
[2] https://en.wikipedia.org/wiki/PIDcontroller.
[3] http://www.pacontrol.com/PID.html.
​
​

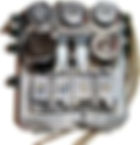


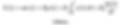


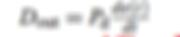
